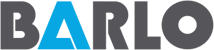
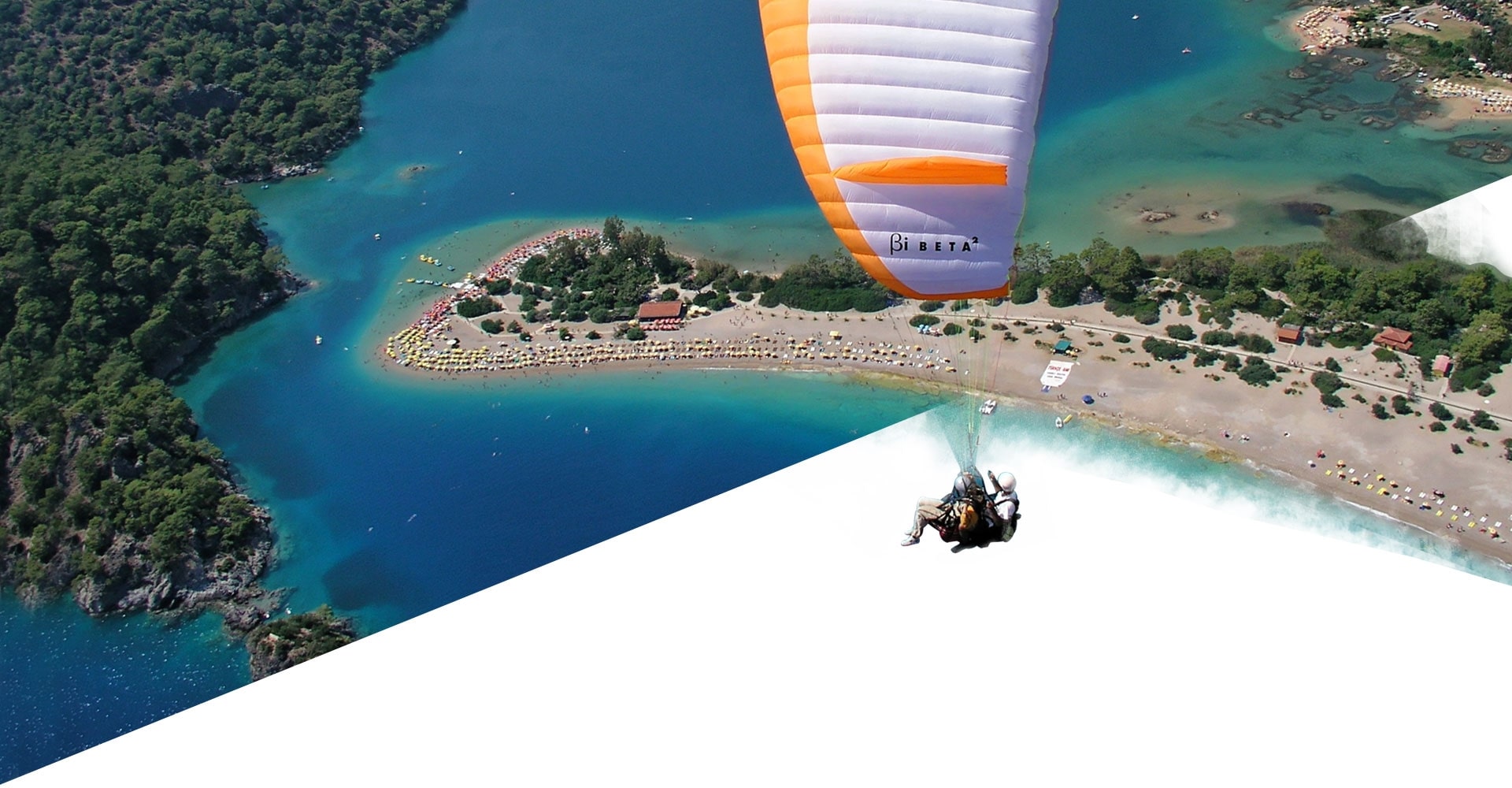
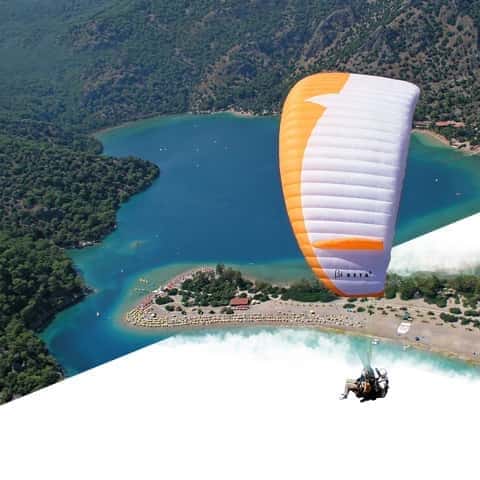
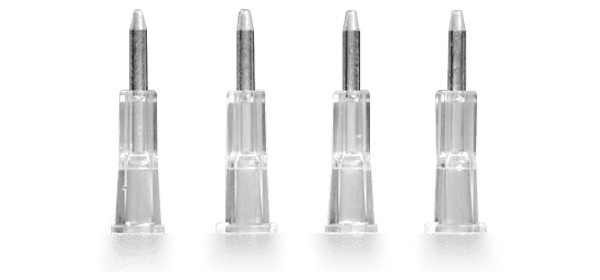
Clean-Room
For a long time, clean-room technology has no longer been a synonym exclusively for the production of medical products, semiconductors or microchips. Increasingly, other technical applications pose increased cleaning requirements on the production environment – be they moulded parts with particularly demanding surfaces or parts with sensitive microstructures. Regardless of that, many moulders have now realized that particularly “clean”, i.e. largely dust-free, ambient conditions have a positive influence on the quality of the formed parts produced and, thus, on the cost-effectiveness of the production. The requirement, however, is always that the individual steps taken are in an economical relationship to the intended purpose. In other words: The product determines the ambient conditions.